胶体磨骨泥(通常指动物骨泥或类似高黏度胶体物料)的高效连续生产涉及工艺优化、设备选型和自动化控制等多环节协同。以下是实现高效连续生产的关键要点:
1. 预处理阶段
原料预处理:
新鲜骨料需经清洗、破碎(≤3cm)和预煮(脱脂、灭菌),减少后续胶体磨负荷。
可通过连续式清洗机和螺旋输送机实现原料的自动进料,确保供料稳定性。
2. 核心粉碎与均质化
胶体磨选型与配置:
选用多级串联胶体磨:粗磨(间隙50100μm)→ 精磨(间隙1020μm),分阶段降低粒径至微米级(D90≤20μm)。
推荐高剪切胶体磨(转速≥3000rpm),配合冷却夹套(控温≤40℃)防止蛋白质变性。
连续供料系统:
采用螺杆泵或柱塞泵输送骨料,避免流量波动;搭配缓冲罐平衡前后工序产能。
3. 在线灭菌与保质
集成UHT或巴氏杀菌:
在胶体磨后串联管式灭菌器(℃/46s),杀灭微生物的同时保持流动性。
实时温度传感器反馈调节,确保灭菌效率。
4. 自动化控制
PLC/DCS控制系统:
监控关键参数(流量、温度、磨腔压力、电机负载),自动调节进料速度和磨盘间隙。
异常报警(如堵料、过热)触发紧急停机,减少废品率。
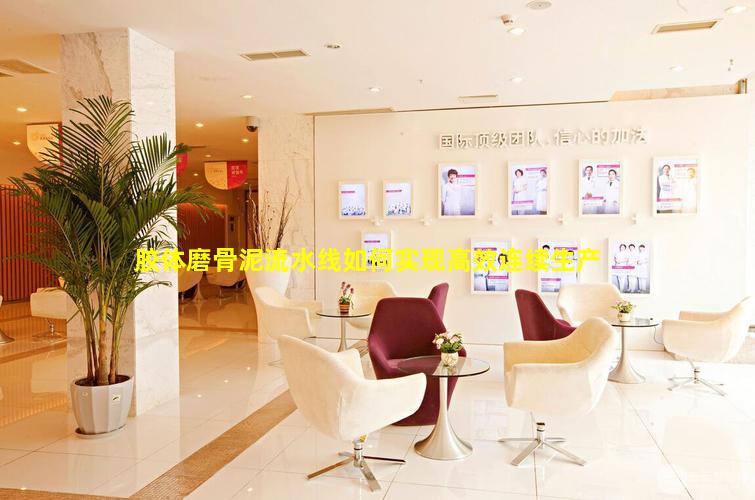
5. 后处理与包装
连续脱水(可选):
若需低水分骨泥,可接入卧螺离心机或真空带式过滤机,同步回收骨汤。
无菌灌装线:
采用伺服驱动的定量灌装机,配合CIP(就地清洗系统),实现24/7连续生产。
6. 效率提升关键点
防堵设计:
管道倾角>45°,磨腔入口加装反冲装置,定期脉冲清洗。
能耗优化:
变频驱动电机+能量回收系统(如余热用于预煮工序)。
数据追溯:
MES系统记录生产批次参数(粒度、微生物等),便于质量回溯。
案例参考某肉类加工厂采用两级胶体磨+在线灭菌流水线,产能提升40%,骨泥细度CV值<5%,单位能耗降低18%。
通过上述设计,可实现骨泥生产从间歇式升级为高效连续化模式,显著提升产能与一致性。需根据原料特性(如含脂量、骨硬度)进一步调试参数。