模具激光焊修复技术在实际应用中虽然具有高精度、低热影响等优势,但仍面临以下挑战:
1. 材料匹配性与冶金相容性
材料多样性:模具钢材种类繁多(如H13、P20、不锈钢等),不同材料的焊接性差异大,需针对性选择激光参数和填充材料。
冶金缺陷风险:快速熔凝可能导致气孔、裂纹(尤其高碳钢的冷裂纹)、成分偏析等问题,需优化工艺或预热/后热处理。
2. 工艺控制难度高
参数敏感性强:激光功率、扫描速度、光斑直径等需精确匹配,微小偏差易导致未熔合或过烧。
三维复杂形状适配:曲面或深槽模具的激光聚焦和送丝路径规划复杂,需机器人或五轴联动设备支持。
3. 残余应力与变形
局部高热梯度:尽管热输入低,但快速冷却可能引发残余应力,影响尺寸精度或导致后续开裂,需通过分段焊接或热处理缓解。
4. 修复质量一致性
缺陷检测要求高:微小气孔或微裂纹需借助X射线、超声波等无损检测,成本较高。
重复性挑战:多批次修复时,环境(如湿度、保护气体纯度)和人为操作可能引入波动。
5. 设备与成本限制
高投入成本:高端激光器(如光纤激光)、精密运动系统和实时监测设备初期投资大。
维护与技术门槛:光学组件易污染,需定期维护;操作人员需兼具激光工艺和模具知识的专业培训。
6. 应用场景局限性
厚大件修复效率低:深缺陷修复需多层堆焊,效率可能低于传统电弧焊。
表面处理要求:锈蚀、油污或氧化层需彻底清理,否则易产生焊接缺陷。
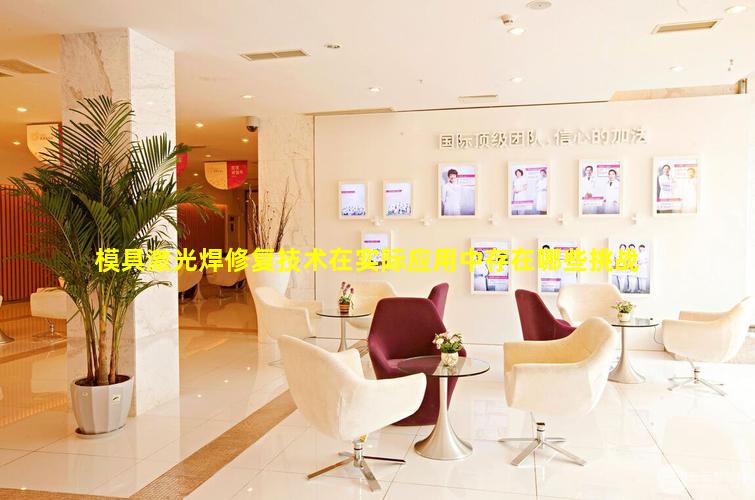
应对措施与发展方向
智能化工艺优化:结合AI和数字孪生技术预测最佳参数。
复合技术应用:如激光电弧复合焊以提升效率,或配合增材制造修复大面积缺损。
新型材料开发:专用焊丝(如纳米改性粉末)以改善冶金性能。
在线监测技术:集成红外热像仪或光谱仪实时调控工艺。
总体而言,激光焊修复技术在模具维护中潜力巨大,但需结合具体工况权衡成本、效率与质量,并持续优化工艺链。