数控激光无痕修复技术确实可以在许多情况下实现高度接近“无痕”的修复效果,但能否达到完全无痕取决于多个因素,需要结合具体应用场景和技术局限性来综合判断。以下是关键分析:
1. 技术原理与优势
精准控制:通过数控系统和高能量激光束,可精确作用于材料表面(如金属、塑料等),逐层熔化或汽化损伤区域,避免对周围材料的热影响。
微米级修复:激光聚焦光斑可小至微米级别,适合修复细小划痕、裂纹或局部磨损。
材料兼容性:适用于高附加值金属(如模具、航空航天部件)或精密电子元件,修复后能保持原有机械性能。
2. 实际修复效果的局限性
材料差异:
金属:修复后可能需抛光或再处理才能完全消除痕迹,尤其是深裂纹或大面积损伤。
塑料/涂层:热敏感材料易因激光产生轻微色差或纹理变化。
损伤程度:
浅表划痕(<0.1mm)通常可接近无痕;深坑或结构变形可能需要补焊后打磨,难以完全隐形。
工艺参数:激光功率、扫描速度等设置不当可能导致过度烧蚀或残留熔渣。
3. 行业应用中的“无痕”定义
工业标准:在模具修复、汽车零部件等领域,“无痕”通常指肉眼不可见且不影响功能性,但显微镜下可能仍有痕迹。
消费电子:如手机外壳修复,需配合后续处理(如阳极氧化、喷砂)才能达到视觉一致性。
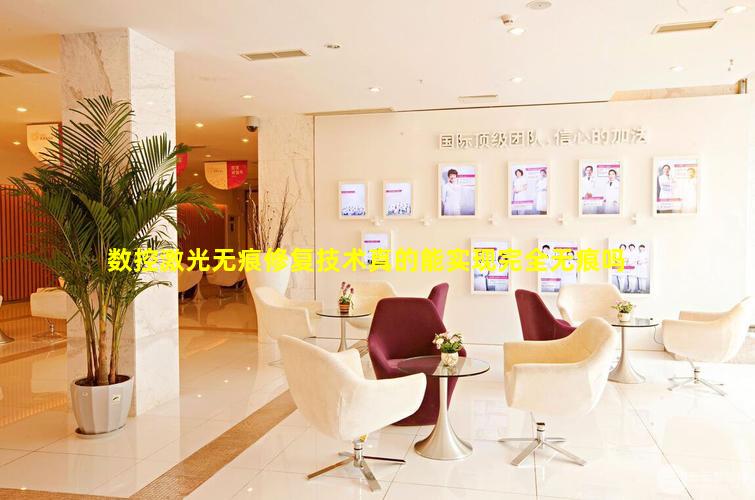
4. 与其他技术的对比
传统焊接:易留下焊疤,需大量后处理。
冷焊/纳米沉积:适合极薄层修复,但效率低于激光。
结论:激光修复在可控性和效率上领先,但“完全无痕”需结合后续工艺。
5. 用户决策建议
评估需求:若追求绝对无痕(如艺术品修复),需小范围测试并配合手工抛光。
选择服务商:优先选择有同材质案例的技术供应商,要求提供修复前后的显微对比图。
成本权衡:高精度激光设备成本较高,适合高价值工件,普通物品可能不经济。
:数控激光无痕修复能实现“近乎无痕”,尤其在微观层面优于多数传统方法,但受材料、损伤深度和工艺限制,完全无痕需具体分析。建议在实际应用前进行试样验证。